Nowadays, more and more attention is invested on improving the manufacturing operations in the industry. With the increasing influence of IoT & AI on our daily life, software used for manufacturing industry is witnessing constant technology advancements as we speak. In addition to a large variety of software (which usually provides CAD/CAM solutions), the digital twin is surely a unique solution for its users.
By providing a real-time and flexible simulation of the machines/products, Digital Twin is affecting the whole product lifecycle management, from manufacturing to transportation, to providing service to the customer. Currently, PLM acts as an essential part of every industry but at the same time, hold its drawbacks like being time-consuming in terms of efficiency, manufacturing, intelligence, service phases and sustainability in product design. A digital twin can combine the real product with its virtual counterpart that enables companies to calculate the product life from design to development and throughout the entire product life cycle.
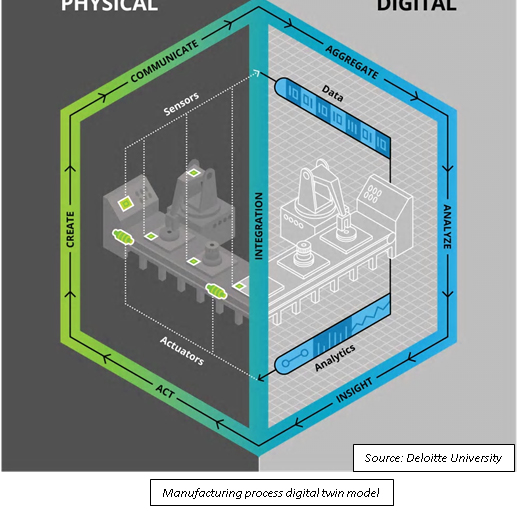
APPLICATIONS
- With digital twin software, user can create a machine or product in a virtual environment before the actual machine exists
- Digital Twin can be used to validate and take control of the CAD model which is connected to the PLC software
- Having a realistic virtual platform for Machine Learning makes the system unique. It reduces Time to Market & production cost of the product
HOW TO CREATE A DIGITAL TWIN
- UPLOAD DATA: Insert 3D CAD model
- PROVIDE COMPONENTS: Select and provide the components of the system
- PROVIDE BEHAVIOUR: Create and provide behaviour of the components
- CONNECTING PLC: Connect the Digital Twin to PLC
- VALIDATION & TESTING: validate and test the Digital Twin of the system in the Virtual environment
INDUSTRIAL APPLICATIONS
MANUFACTURING
For the manufacturing industry, Digital Twin is the most resourceful and incessant real-time development platform for visualizing products and machines. In the manufacturing process, the digital twin is like a virtual replica of the real-time working in the factory. Multiple sensors are being used throughout the physical manufacturing process, all collecting data from different dimensions, such as environmental conditions, behavioural characteristics of the machine and work that is being performed. All this data is continuously communicated and collected by the digital twin.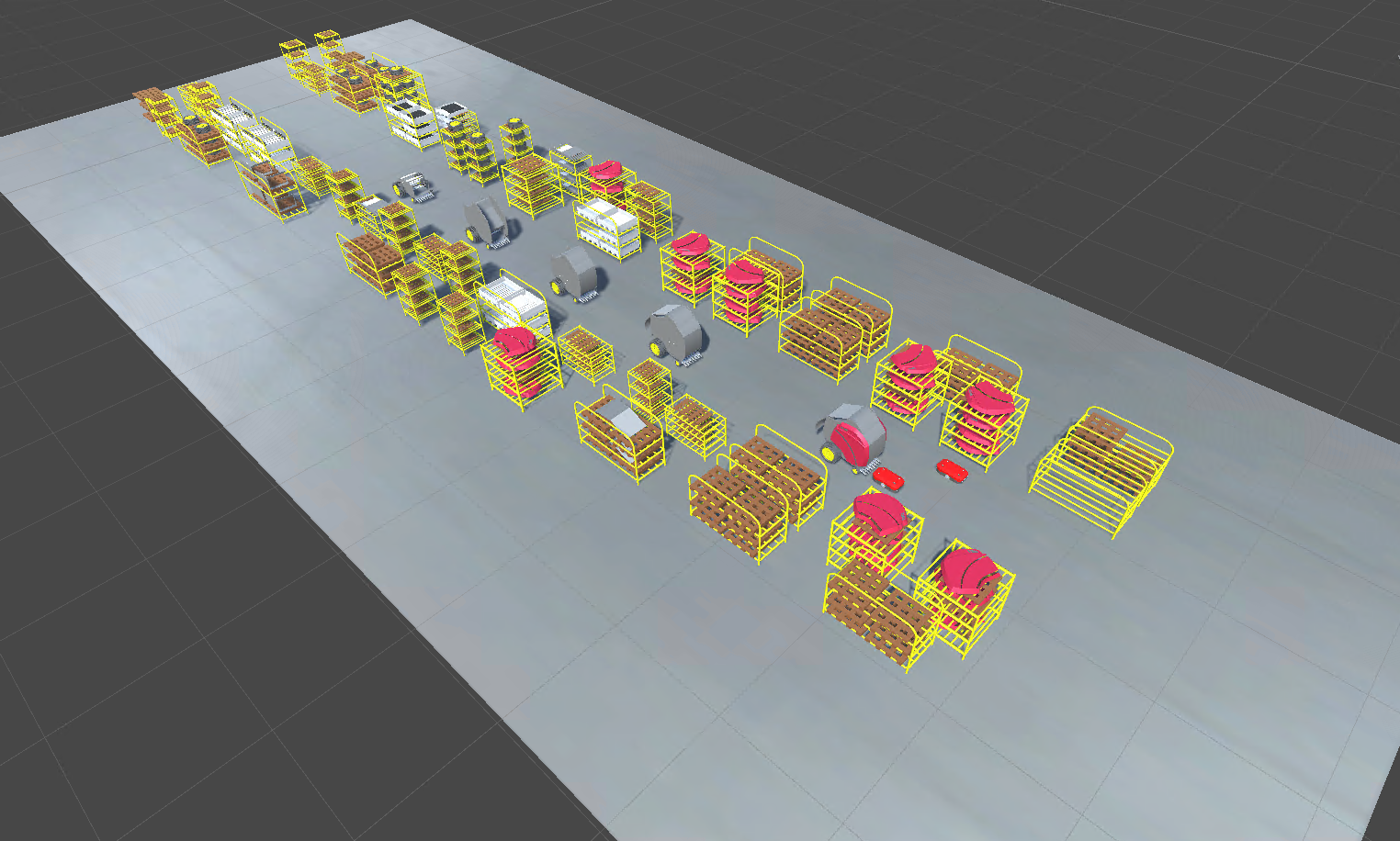
AEROSPACE
A digital twin which is functioning at its full capacity can provide a predictive and comprehensive analysis. For instance, with this technology risk of future engine failure can be easily accessed utilising the available past data.
INFRASTRUCTURE
A digital twin, capitalizing on its design and features allows users to experience an environment before it exists, and accordingly, train people without thinking about the physical constraints.
TRANSPORTATION
For developers, engineers, and mechatronics across the transportation industry, a digital twin is the most versatile and stable real-time development platform for building interactive and virtual machinery.
ADVANTAGES
VIRTUAL SYSTEM VALIDATION
Digital Twin enables a user to test any system in a virtual world. It allows the user to test their assumptions since the geometry is connected to the PLC software. This way, the user has a communication tool between multiple disciplines such as engineering, mechatronics and software development. The virtual model can further be enriched with all sorts of data feeds; building own inversed kinematic system, creating the ideal MDE toolkit.
VIRTUAL PROTOTYPING
By adding logic to the CAD model, we can make the system come to life in a matter of minutes. The Virtual Prototype will have the exact same behaviour as a first hardware prototype, thus creating a shorter time to market. Driven by the real control software (connected to any type of PLC) the failure costs will also be drastically reduced.
COLLISION DETECTION
In a plant or production line, detection of collisions between objects and robots is always necessary. For this requirement, a user can use colliders. Using a digital twin, we can set up a software failsafe instead of a hardware failsafe.
CONCLUSION
Hence, to conclude, it is safe to say that creating a Digital Twin provides the user with a fully functioning machine in a desired virtual environment. Among the advantages mentioned above, this provides real time data to the user that further helps in saving the cost of manufacturing and unnecessary rework.